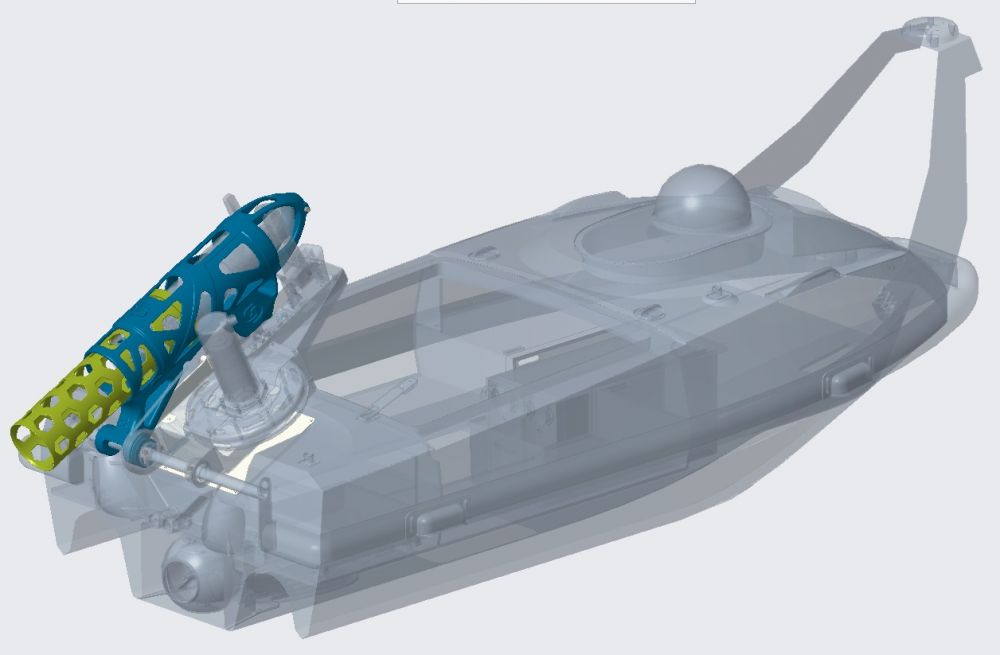
Contexte du projet de Fabrication Additive de pièces série
Le leader de la fabrication additive Ricoh 3D s'est associé aux experts en génie mécanique de Mécastyle pour tester son polypropylène (PP), en tant que matériau pour les applications en série.
Après s'être rencontrés lors d'une conférence de l'industrie, Ricoh 3D et Mécastyle ont concrétisé leur vision commune en aidant les clients à faire passer la fabrication additive du prototypage à la production de pièces en série.
Enrico Gallino, spécialiste des matériaux chez Ricoh 3D, a déclaré: «Nous savions tous instantanément qu'il y avait une réelle synergie stratégique ici, alors quand Mécastyle nous a contactés avec le projet Cadden , nous étions tous les deux ravis de voir ce que notre expertise combinée pouvait accomplir.»
Arrière-plan
Ocean Alpha SL40 est un bateau d'analyse autonome hautement sophistiqué développé par les spécialistes des applications marines Cadden. L'USV (Unmanned Surface Ship) de 1,6 mètre de long est un système de relevés hydrographiques unique utilisé pour la détection et l'identification des objets et la classification des fonds marins, fournissant également un contrôle visuel sous l'eau et en temps réel pour surveiller les travaux ou la sécurité du site.
Cadden a travaillé avec Mécastyle pour concevoir et produire avec succès une solution innovante de verrouillage, de libération et de récupération des sondes en déployant tous les avantages de la fabrication additive (FA), plus communément appelée impression 3D.
En exploitant les caractéristiques du matériau issues de son propre laboratoire d'essais, Mécastyle a conçu une solution série qui permet d'atteindre un véritable «Design for Additive Manufacturing» (DfAM).
Le besoin
Développeur, fournisseur et exploitant de systèmes de géolocalisation et d'hydrographie, Cadden avait besoin d'équiper son USV (Unmanned Surface Vehicle) d'un système de verrouillage, de libération et de récupération d'une sonde.
Thomas Péan, à propos du polypropylène de Ricoh : «Nous savions qu'il n'y avait pas d'informations disponibles sur les performances en fatigue des Matériaux Additifs et avons contacté Ricoh pour son expertise dans la production de pièces fonctionnelles. La combinaison de nos compétences en caractérisation mécaniques, en conception de pièces, en ingénierie et en production de pièces nous a permis de générer dans notre laboratoire d'essais les mêmes données normalement disponibles concernant les processus de fabrication traditionnels».
Comme il s'agissait d'une pièce complexe produite initialement en faibles volumes, le processus de frittage sélectif par laser était le mieux adapté en raison de la grande chambre de fabrication du système Ricoh, ce qui signifiait que toutes les pièces pouvait être imprimées simultanément en un seul ensemble et déjà assemblées au cours du processus de fabrication additive.
La solution
Associer l'expertise de Mécastyle en ingénierie mécanique et les capacités de production de Ricoh pour répondre aux besoins de Cadden.
1. Analyse fonctionnelle
Comme pour tout projet mécanique, l'analyse fonctionnelle a été la première phase réalisée. Cette phase consiste à identifier, hiérarchiser et décomposer les principales fonctions et contraintes du produit pour atteindre les résultats souhaités. Réalisée avant la conception, l'analyse fonctionnelle constitue la pièce angulaire de la réussite du projet.
Cette analyse fonctionnelle a abouti au choix d'un matériau polymère, en réponse aux fonctions de contraintes de masse et de résistance à l'environnement.
La fonction de contrainte de masse a exclu l'utilisation de matériaux métalliques denses.
La fonction de contrainte de résistance au milieu aquatique a éliminé l'utilisation de polymères à forte absorption d'humidité ou sensibilité à l'hydrolyse.
2. Essais en fatigue
L'étude du potentiel de résistance à la fatigue d'une pièce ou d'une structure consiste à contrôler le comportement du matériau à partir d'essais sur éprouvettes. Ces tests sont réalisés dans le laboratoire d'essais en fatigue de Mécastyle.
Les caractéristiques issues de ces tests sur éprouvettes permettent de prédire par calcul de structure le comportement des pièces ou produits conformément au procédé de fabrication additive, de concevoir et d'optimiser topologiquement autour de ces paramètres.
On a constaté un comportement en fatigue très favorable du polypropylène Ricoh au regard des contraintes induites, à un prix très rentable et, surtout pour l'application, sans absorber d'eau. Avec un PA12, une étape supplémentaire était nécessaire pour imprégner ou peindre la pièce, ce qui entraînait un processus plus long et plus coûteux.
Le polypropylène a donc été considéré comme le matériau le plus approprié pour cette application.
3. Coût - analyse économique
Le coût étant une autre fonction de contrainte, une analyse économique a été réalisée pour déterminer le procédé de fabrication répondant au mieux aux exigences de notre client (Design to Cost), c'est-à-dire une production en faible volume (quelques dizaines d'unités par an), fabriquée à la demande et sans gestion des stocks. Les deux processus les plus pertinents pour cela sont l'usinage et la fabrication additive.
Étant donné le potentiel d'intégration de fonctions offert par la fabrication additive, ce processus s'est avéré être le meilleur compromis technico-économique pour le projet Cadden. Le coût de l'ensemble imprimé simultanément en 3D en polypropylène Ricoh SLS, est près de 2 fois moins élevé par rapport à une solution usinée.
Thomas a commenté: «En plus de l'avantage de réduction des coûts de production, la fabrication additive permet de produire des pièces à la demande. C'est un avantage clef notamment au regard de l'absence de financement des stocks.»
4. Valeur ajoutée du matériel Ricoh
«Les propriétés d'étanchéité de notre polypropylène sont uniques sur le marché aujourd'hui», a expliqué Enrico. «Cela signifie qu'aucun post-traitement n'est nécessaire pour fabriquer une pièce esthétique et étanche, ce qui rend le projet viable pour le prototypage jusqu'à la production en série.»
5. Conception pour la fabrication additive
Pour réaliser la gamme complète des avantages de la fabrication additive, la solution Mécastyle a été conçue en utilisant la méthodologie ''Design for Additive Manufacturing'' (DfAM), méthodologie de conception entièrement orientée vers la fabrication additive pour inclure l'intégration des fonctions, l'optimisation topologique, la fusion des pièces pour limiter l'assemblage, la personnalisation et l'intégration de l'image de marque.
En caractérisant le polypropylène de Ricoh à des contraintes cycliques, les composants sont alors conçus et calulés en utilisant ces données mécaniques recueillies comme spécification.
6. Calcul et simulation pour améliorer le temps de mise sur le marché
Parallèlement à cette phase d'étude, la simulation numérique (Calcul de structure par éléments finis) a permis à Mécastyle d'anticiper le comportement du produit en fonction des contraintes mécanique subies. Cette étape permet de converger rapidement vers une définition numérique conforme aux spécifications fonctionnelles du client, ce qui se traduit par une réduction significative des délais de mise sur le marché des pièces série. Cela permet également de réduire le nombre de prototypes fonctionnels à tester sur banc, et donc les coûts induits.
En détail
En fonction des efforts à appliquer dans les pièces, les simulations numériques par calcul de structure sont utilisées pour déterminer les contraintes mécaniques dans les pièces et prédire très rapidement leurs comportements. Cette méthode est très efficaces par rapport au cycle de développement classique des pièces qui implique des itérations de fabrication - tests sur banc - modifications - fabrication - nouveaux tests, avec les coûts et délais induits.
Toutes ces données permettent l'optimisation de la conception en termes de section matière (donc poids) et géométries. L'optimisation de la conception génère des formes organiques possibles en fabrication additive, visuellement appréciables tout en garantissant les performances requises. Cette combinaison de données quantitatives et qualitatives produit des pièces fonctionnelles et rentables, qui peuvent encore être fabriquées grâce à la liberté de conception de la fabrication additive et du processus de frittage laser sélectif en particulier. Les mêmes performances auraient été impossibles avec le processus de dépôt de fil, l'enlèvement de matériau de support devant également être pris en compte dans le cadre de ce processus.
Le frittage sélectif par laser (SLS) , également connu sous le nom de ''fusion sur lit de poudre'', est considéré comme la technologie de base des fournisseurs d'impression 3D en raison de sa productivité et de sa large gamme de thermoplastiques techniques. De plus, l'absence de substrat en fait le choix idéal pour la fabrication de formes complexes, comme le porte-sonde Cadden.
Livraison
Pour cette application, la fabrication additive est beaucoup plus rapide et plus réactive que les méthodes traditionnelles de fabrication, car les outillages associés ne sont plus nécessaires.
Thomas a conclu: «Les avantages de la fabrication additive nous ont permis d'offrir à notre client Cadden la meilleure solution série clef en main répondant aux exigences fonctionnelles, techniques, économiques et délais.»